Третьего июля исполнилось шестьдесят лет с тех пор, как первая доменная печь Карагандинского металлургического завода выдала первый казахстанский чугун. Со временем предприятие лишь набрало обороты – сегодня это металлургический гигант – комбинат АО «АрселорМиттал Темиртау».
Истоки железной реки
В 1930 годы К. Сатпаев, М. Русаков и А. Сперанский детально изучали месторождения железных руд Центрального Казахстана. Именно эти ученые и выдвинули идею о строительстве металлургического предприятия посреди казахстанской степи, а начавшаяся вскоре Великая Отечественная война лишь укрепила эти убеждения.
Государственный Комитет обороны в 1942 году принял решение о строительстве небольшого передельного завода недалеко от Караганды. В голой степи кирками и лопатами был построен Казахский металлургический завод, который и стал начальной точкой развития казахстанской металлургии. В декабре 1944 в разливочный ковш мартеновского цеха хлынула первая казахстанская сталь, через год поселок Самарканд стал городом Темиртау, а спустя 16 лет уже начал работу металлургический гигант – 3 июля 1960 года первая доменная печь выдала казахстанский чугун! И сегодня металлургический комбинат АО «АрселорМиттал Темиртау» по-прежнему остается флагманом казахстанской металлургии, опорой экономики страны и градообразующим предприятием для Темиртау.
Место строительства было выбрано не случайно: близкое расположение коксующихся углей Карагандинского угольного бассейна, известняк Топара, Атасуйское и Жездинское месторождения железныхи марганцевых руд, река Нура и возможность создания Самаркандского водохранилища сыграли свою роль.
Строительство Казахстанской Магнитки началось в мае 1943 года с постройки Казахского металлургического завода. Чертежи и проектное задание были подготовлены сотрудниками свердловского отделения Гипромеза. Сначала на стройку прибыли специализированные организации Наркомстроя, затем в короткий срок были подготовлены и аттестованы квалификационной комиссией 1300 человек по самым необходимым строительным специальностям и мобилизовано еще три тысячи человек. Началом строительства завода считается осень 1950 года. Так как стройка была объявлена всенародной, в Темиртау начали стекаться молодые люди со всего Советского Союза. В 1956 году столица Казахской ССР Алма-Ата проводила первую группу комсомольцев и молодежи, а через год в город металлургов прибыла бригада в составе 1070 посланцев Народной Республики Болгарии для участия в возведении промышленных объектов завода и строительстве жилых и бытовых объектов для города.
Хлынул первый чугун
Торжественная закладка доменной печи №1 состоялась в декабре 1957 года. Третьего июля 1960-го печь выдала первый казахстанский чугун. Плавкой тогда руководил Вадим Романов, старшим горновым был Ахат Набигулин. Вместе с опытными мастерами в плавке первого казахстанского чугуна участвовал молодой металлург Нурсултан Назарбаев — будущий Первый Президент Республики Казахстан. Казахстанская Магнитка сыграла огромную роль в судьбе Нурсултана Абишевича. Здесь не только началась его трудовая деятельность, тут проходило становление его как личности и профессионала. Нурсултан Назарбаев не раз говорил: «История Магнитки, история Темиртау, судьба его людей неотделимы от моей судьбы. Если бы в моей жизни не было Магнитки и Темиртау, я бы никогда не стал Президентом».
В этом же году был получен первый казахстанский кокс, а год спустя первый чугун выдала доменная печь №2.
С 1961 по 1970 год в эксплуатацию ввели многие промышленные объекты, важные для металлургического производства полного цикла: аглофабрика №1, смолоперегонный цех КХП, мартеновский цех, фасонно-литейный цех, ЦОИ-1, копровый цех, углеобогатительная фабрика №1, ЛПЦ-1 (стан горячей прокатки 1700), ЦРМО-3 и другие. В 1970-м введен в эксплуатацию первый 250-тонный конвертер. В этом же году на базе Карагандинского металлургического завода был образован Карагандинский металлургический комбинат, в состав которого вошли Казахский металлургический завод, Атасуйское и Южно-Топарское рудоуправление и Алексеевский доломитовый карьер.
Ну а затем по нарастающей для увеличения объемов производства начали один за другим вводиться в эксплуатацию производственные объекты: 1971 год — доменная печь №3, 1973-й — цех холодной прокатки листа, 1975-й — аглоцех №2 и доменная печь №4.
В 60-70-е годы активно развивались не только промышленные объекты, но и социальные. В приоритете у государства стояла комфортная жизнь металлургов, которая позволяла бы им трудиться и отдавать себя профессии целиком. За это время построили крупнейшую в республике медсанчасть со стационаром, завод-ВТУЗ, комбинат питания, цех бытового обслуживания, металлургический техникум, плавательный бассейн и детский парк.
6,2 млн тонн стали в год
Кто лучше, чем ветераны производства, смогут рассказать, как развивался и чем жил комбинат в доперестроечные годы. Вспоминает бывший директор по производству АО «АрселорМиттал Темиртау» Виктор Адякин, чей общий рабочий стаж составляет 39 лет:
— Учился я с Олегом Сосковцом во ВТУЗе по специальности ОМД. После его окончания, в 1971 году, мы так же вместе пришли вальцовщиками в ЛПЦ-2 и стали участниками запуска в эксплуатацию листопрокатного цеха №2 в составе стана прокатки холоднокатаного листа. Было это 22 июня 1973 года. На запуск были приглашены специалисты из Череповца, Жданова и Магнитогорска. Мы учились у этих людей на первом этапе становления вальцовщиками. Благодаря их опыту темиртаусцы в дальнейшем смогли производить самостоятельный процесс прокатки холоднокатаного металла и добиваться серьезных показателей. На тот момент стан холодного проката ЛПЦ-2 был по мощности четвертым в Советском Союзе с объемом производства 1 млн 300 тысяч тонн проката в год. Каждые полгода мы ездили в Министерство черной металлургии и защищали планы на полугодие и год. Госплан утверждал объемы и сортамент холоднокатаного листа, которые требовались народному хозяйству СССР. Спрос был 100%. Я в ЛПЦ-2 дорос от вальцовщика до начальника цеха, и в этот же период мой однокурсник Олег Сосковец возглавил Карметкомбинат в должности генерального директора. На моих глазах происходило становление всего коллектива, рос завод. И даже в тяжелые годы люди болели душой за любимое дело. Именно благодаря им сегодня комбинат продолжает жить, а вместе с ним продолжает развиваться и город Темиртау.
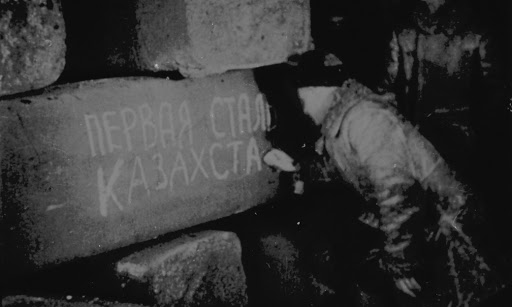
В 1975 году юным пареньком на комбинат пришел Михаил Витущенко. Начинал он инженером ЦЗЛ, затем руководил агломерационной группой. С 1995 по 2004 был начальником центральной теплотехнической лаборатории, затем возглавлял технический отдел комбината, а с 2007г комбината был назначен генеральным менеджером по качеству. Последние пять лет, будучи на заслуженном отдыхе, Михаил Витущенко работает техническим консультантом на АО «АрселорМиттал Темиртау».
— Когда по окончанию Завода – ВТУЗА я получил распределение на комбинат, в это время запускалась аглофабрика №2, в связи с чем расширялась агломерационная лаборатория ЦЗЛ, где мне предложили должность инженера, — вспоминает Михаил Федорович. — Раньше агломерационное производство состояло из двух агломерационных фабрик. Первый чугун получали на атасуйской руде, без участия агломерата. В то время были уже свои коксовые батареи. С запуском второй и третьей доменных печей резко обострился вопрос по обеспечению доменного цеха сырьем. В комплексе со строительством четвертой доменной печи (самой крупной на комбинате – 3200 м3) была спроектирована и построена аглофабрика №2 на 6,0 млн тонн в год агломерата под сырье Лисаковского месторождения.
Это сейчас в аглопроизводство комбината входит ДСФ и аглофабрика, тогда же в его составе было четыре цеха: аглофабрики №1 и №2, дробильно-сортировочная фабрика и цех обезвоживания шламов. И трудилось здесь более 2000 человек. Проблем с освоением фабрики хватало, связано это было в первую очередь со спецификой фосфористого железорудного сырья. Но квалифицированные работники комбината успешно справились с поставленной задачей. В 1983 г. пять сотрудников комбината в составе авторского коллектива были удостоены звания «Лауреат Государственной премии СССР в области науки и техники» за освоение технологии металлургического передела фосфористых руд Лисаковского месторождения. За счет организации двух раздельных технологических потоков на переделе аглофабрика- доменный цех- сталеплавильные цехи (мартеновский цех №1, конверторный цех) и освоения технологии передела высокофосфористых чугунов в большегрузных конверторах, в конце 80-х — начале 90-х годов были достигнуты максимальные объемы производства стали 6,2 млн тонн в год.
Шаг в правильном направлении
После распада СССР к середине 90-х Карагандинский металлургический комбинат находился в сложном положении. Производственные мощности предприятия требовали ремонтов, запасы основных материалов и необходимых запасных частей были почти на нуле. Традиционные источники поставок в странах СНГ прекратили свое существование, а рынок конечной продукции стал носить бартерный характер.
С начала 1995 года активы ГАО «Кармет» перепродавались дважды. В ноябре этого же года было объявлено о том, что международная компания «ЛНМ-групп» приобрела металлургический комбинат, названный впоследствии «Испат-Карметом». Сегодня предприятие носит название АО «АрселорМиттал Темиртау».
Первые два года были для предприятия самыми трудными. Тем не менее, руководству компании вместе со всеми работниками комбината удалось их преодолеть. Во второй половине 1997-го на комбинате наблюдается рост производства. Чугуна в этот год выдано 3 млн 89 тысяч тонн, стали – 3 млн 22 тысячи тонн.
Чтобы избежать в будущем проблем с топливом и электроэнергией, руководство предприятия в 1996 году приобретает ТЭЦ-2 и угольные шахты. А с 2000-го компания «АрселорМиттал Темиртау» становится недропользователем четырех железорудных месторождений.
С самого начала работы выделено четыре основных направления деятельности: техническая модернизация, развитие и укрепление рынка, обучение персонала и корпоративная социальная ответственность.
Первой ласточкой стала замена старых линий травления во втором листопрокатном цехе. Работы были завершены в мае 1998 года. В этом же году на металлургическом комбинате запущен первый новый цех – цех горячего алюмоцинкования. На тот момент это был самый передовой цех. Зимой 2001 года введена в строй вторая линия ЦГЦА.
В течение следующих четырех лет руководство предприятия ведет планомерную работу по модернизации оборудования, подготавливая основные цеха к работе с непрерывнолитыми слябами. В это же время производится капитальный ремонт доменной печи №3. В результате реконструкции увеличились объемы производства чугуна.
Вслед за 3-ей доменной печью капитальный ремонт произвели и на четвертой домне. Модернизации подвергнута система управления печью, увеличен объем выплавки чугуна.
В начале 2005 года первая машина непрерывного литья заготовок выдала первый сляб. В конце этого же года запущена и вторая машина. С этого момента комбинат полностью перешел на новую технологию разливки стали.
— Когда я пришел на комбинат в 1969 году, можно сказать, завод наращивал свои объемы, — рассказывает ветеран комбината, бывший старший директор по производству и капстроительству Виктор Щерба. — Тогда еще работала старая технология: разлив металла производился в изложницы, затем слитки поступали в обжимной цех, где после нагрева прокатывались в слябы. Первое технико-экономические обоснование строительства МНЛЗ было разработано в начале 90-х. По разным причинам внедрение проекта откладывалось. Лишь в 2005 году линия все-таки была запущена.
Главный плюс в запуске линии – это полмиллиона тонн готовой стали, которая раньше уходила в обрезь. Кроме того, это улучшение качества продукции, расширение сортамента выплавляемых марок стали, энергосбережение, повышение безопасности труда и экологическая безопасность. После запуска отпала необходимость в цехе изложниц, в обжимном цехе и цехе подготовки составов. Сначала МНЛЗ-1 производила серию из 6-8 плавок. Сегодня, благодаря дальнейшей модернизации, серия плавок, разлитых на один промковш, достигает 14. На данный момент в конвертерном цехе работает три машины непрерывного литья заготовок: две слябовых, а третья выпускает сортовые заготовки — блюмы.
И, конечно, не могу не
сказать о людях, чей огромный вклад в развитие производства и упорный труд позволили
комбинату наращивать мощности и улучшать качество продукции. В одно время со
мной трудились главный механик Николай Манжос, главный энергетик в то время
Вадим Басин, главный сталеплавильщик Владимир Богомяков, начальник аглопроизводства
Геннадий Бутенко, начальник доменного цеха Александр Печёркин.
В 2005 году АО «АрселорМиттал Темиртау» начало реализацию еще двух проектов:
реконструкцию коксовой батареи №7 и возведение цеха покраски.
В июне этого же года главой государства был заложен первый камень в фундамент комплекса сортопрокатного производства, предназначенного для удовлетворения потребностей казахстанской строительной индустрии. Первая продукция была получена спустя три года.
Компания «АрселорМиттал Темиртау» продолжает уделять большое внимание техническому переоснащению, внедряя современные технологии, направленные на повышение качества выпускаемой продукции и увеличение ее конкурентоспособности, ежегодно инвестируя миллионы тенге в развитие производств.
Модернизированы три доменные печи, обновляются основные производственные мощности агломерационного и коксохимического производств. Проведена реконструкция оборудования сталеплавильного и прокатного переделов. Завершен в 2019 году проект по установке печь-ковш №3, который позволит увеличить объемы производства стали. Внедрение современных технологий сделало производство стали более безопасным, экологичным и эффективным.
Полный цикл сегодня
Несмотря не на что, комбинат с момента запуска в эксплуатацию не на минуту не останавливал свою работу. Благодаря проведенным модернизациям производственные мощности основных технологических агрегатов сохраняются на достаточно высоком уровне. На сегодня производственная мощность коксохимического производства (КХП), в состав которого входит шесть коксовых батарей, составляет 2,8 млн тонн кокса в год. В 2017 году был достигнут максимум в производстве – 2,6 млн тонн кокса. Годовая мощность аглопроизводства составляет 5,9 млн тонн агломерата. Максимальное годовое производство агломерата было достигнуто в 2007 году – 6,5 млн тонн.
В составе доменного цеха работают на данный момент три доменные печи, доменная печь №1 выведена из эксплуатации и законсервирована. Производственная мощность на январь 2020 года: доменная печь №2 – 1033 тысяч тонн/год, доменная печь №3 – 1790 тысяч тонн/год, доменная печь №4 – 1525 тысяч тонн/год. Суммарная мощность доменного цеха составляет 4,3 млн тонн чугуна в год, который отправляется на переработку в конвертерный цех. В планах у руководства АО «АрселорМиттал Темиртау» довести все печи до евростандарта.
Прокатное производство
представлено тремя цехами: ЛПЦ-1, ЛПЦ-2, ЛПЦ-3. Первый производит товарный
горячекатаный прокат в рулонах и листах толщиной от 2,0 до 12,0 мм, штрипс для электросварных труб, а также
обеспечивает подкатом цеха холодного проката ЛПЦ-2 и ЛПЦ-3. Второй производит холоднокатаный прокат
толщиной от 0,4 до 2,0 мм, штрипс для электросварных труб, кровельный прокат.
Третий специализируется на черной и белой жести, производит также кровельный
прокат.
Прокат с цинковым и алюмоцинковым покрытием и окрашенный прокат – это
прерогатива цеха горячего цинкования и алюмоцинкования (ЦГЦА).
В 2008-м был запущен сортопрокатный цех. Он производит арматурный прокат по всем имеющимся стандартам для строительной отрасли Казахстана, а также обеспечивает рынок Средней Азии и России. В 2015 году здесь впервые достигли годовой проектной мощности, прокатав 406 тысяч тонн арматурного проката. В 2017 году – 417 тысяч тонн проката.
— Вообще, 2017 год стал одним из лучших по годовым показателям. Мы достигли отметки производства стали 4 млн 300 тысяч тонн, — делится Михаил Витущенко.
Цели компании в среднесрочной перспективе, при условии благоприятной ситуации на рынке черных металлов, выйти на годовое производство стали 5,0 млн тонн. Несмотря на то, что выведены из эксплуатации два мартеновских цеха, конвертерный цех в состоянии выплавлять и 6,0 млн тонн жидкой стали в год, только для этого необходим чугун соответствующего качества. В настоящее же время, из-за сложившейся общей мировой обстановки усилия компании направлены на снижение производственных затрат и себестоимости производимой продукции. Это максимальное использование собственных сырья и топлива, рациональное использование и генерация внутренних энергоресурсов.
Что касается географии реализации готовой продукции, то 30% объема — это внутренний рынок, остальное отгружается в Китай, Россию, Иран и страны Средней Азии.
Экология – в приоритете
Немалое внимание компания уделяет внедрению экологических проектов. В 1995 году на момент прихода компании «АрселорМиттал» в Казахстан пылегазоочистные установки основных источников загрязнения (электростанции, агломашины, коксовые батареи, доменные печи и сталеплавильные агрегаты) по своей эффективности соответствовали уровню 50-60 годов и не справлялись с объемом выбросов загрязняющих веществ. Проектная стоимость природоохранных структур составляла всего 3-5% от общей стоимости основных производственных объектов. Было очевидно, что старый подход к решению экологических проблем, основанный на выполнении разрозненных мероприятий разового характера, себя полностью исчерпал. И в этой связи на комбинате по инициативе компании с привлечением международных экспертов Банка развития был произведен всесторонний аудит экологической обстановки с целью разработки стратегии коренного изменения сложившейся экологической ситуации, которая впоследствии была реализована.
Провели реконструкцию газоочисток котельного цеха ТЭЦ-ПВС и зоны спекания агломерационного цеха. Вывели из эксплуатации два мартеновских цеха, аглофабрика №1, обжимной цех и цех изложниц. После того как реализация этих масштабных проектов завершилась, в 2004 году было принято решение о реконструкции газоочисток за котлами №5 и №6 ТЭЦ-2, вращающихся печей №1 и №2 ЦОИ.
До 2016 года были установлены электрофильтры для очистки выбросов бункерной эстакады и литейного двора доменной печи №4 и рукавные фильтры для доменной печи №3. Проведена реконструкция системы охлаждения коксового газа в замкнутом цикле, газоочисток за зоной охлаждения агломашин 5-7 агломерационного цеха, электрофильтров за вращающейся печью №3 ЦОИ, газоотводящего тракта конвертеров № 1,2,3 со строительством первичных газоочисток с мокрой системой очистки и рукавных фильтров вторичной газоочистки для трех конвертеров. Реконструировано пылеочистное оборудование ПУ-31 и ПУ-39 корпуса выделения постели агломерационного цеха и известкового отделения шахтных печей ЦОИ, построены рукавные фильтры для миксерного отделения конвертерного цеха.
— Реконструкция существующего
природоохранного оборудования продолжается. Многие проекты имеют сроки
реализации не один год, поскольку ведется замена неэффективно работающего
оборудования сразу на нескольких технологических агрегатах – например, замена батарейных
циклонов на электрофильтры зоны спекания агломашин № 5-7 рассчитана поэтапно на
три года, реконструкция очистных сооружений коксохимического производства — это
фактически строительство нового цеха улавливания химических продуктов с вводом
в эксплуатацию новой биохимии должно быть реализовано за 4 года, — рассказывает
директор по экологии Галина Дроздова. – В доменном цехе приступили к уточнению
технических параметров по проектированию с дальнейшим монтажом 4-х
электрофильтров для доменной печи № 2. Выполняется ряд проектов в
коксохимическом и агломерационном производствах на перегрузочных узлах. И наконец, на комбинате приступили к
реализации главного проекта —
реконструкции котельного цеха ТЭЦ-ПВС, который предусматривает
строительство нового котельного и газоочистного оборудования, сегодня ведутся
демонтажные работы на котле № 1 и дымовой трубы № 1. Экологическая программа
предусматривает не только проекты по охране атмосферного воздуха, что крайне
важно для нашего города, но и по управлению отходами производства и потребления
и т.д. Проект наращивания золошламонакопителя тоже очень важный проект,
готовятся разрешительные документы для реализации следующего его этапа. До 2025
года, как этого требует Правительство, мы должны завершить проект по замене
трансформаторов, содержащих ПХД-отходы на трансформаторы «сухого» типа и
утилизировать их. В планах — проекты по вопросам рационального использования
водных ресурсов, реконструкции оборотных циклов.
— Инвестиции в экологические проекты металлургического комбината с 2017 по
2019 годы составили 18,9 млрд тенге, из них затраты на реализацию
экологических проектов в 2019 году – 7,6 млрд тенге. Планируемые затраты на
реализацию экологических проектов согласно плану природоохранных
мероприятий АО «АрселорМиттал Темиртау» на 2019-2021
годы составляют свыше 35 млрд тенге. Главная цель АО «АрселорМиттал
Темиртау» сегодня – приблизить работу комбината к параметрам
восточноевропейских стран, – говорит исполнительный директор АО «АрселорМиттал
Темиртау» Вадим Басин.
На данный момент разрабатывается проект по переводу комбината на работу на
природном газе, что в свою очередь значительно снизит экологическую нагрузку.
Поддерживая страну и людей
В настоящий момент АО «АрселорМиттал Темиртау» является лидером по казахстанскому содержанию. Каждый год компания подписывает соглашение по целевым индикаторам местного содержания, направленное на импортозамещение закупаемого товара, увеличение несырьевых товаров и запуск новых предприятий в Карагандинской области.
Компания поддерживает бизнес Карагандинской области, и за девять месяцев 2019 года закупило товаров, работ и услуг на сумму 102 миллиарда тенге. Доля местного содержания в общем объёме закупок по товарам с учётом сырья составила 65,61%, без учёта сырья — 31,34%.
Не забывает руководство АО «АрселорМиттал Темиртау» и о людях. По поручению Первого Президента Казахстана между акиматом Карагандинской области и администрацией компании «АрселорМиттал Темиртау» был подписан меморандум на строительство социально важных объектов в городе Темиртау. На данный момент заканчивается строительство полклиники и спорткомплекса на 32-ом квартале. В ближайшее время начнется строительство детского сада в 4а микрорайоне.
Сегодня комбинат продолжает развиваться, большие средства вкладываются в модернизацию оборудования, огромные средства тратятся на усовершенствование производства и технику безопасности, но самое главное — традиции, заложенные шестьдесят лет назад, продолжают жить.
журнал «Горно-металлургическая промышленность» №5-6 2020
Наталья Лукьянова
Фото из архива пресс-службы АО «АрселорМиттал Темиртау»